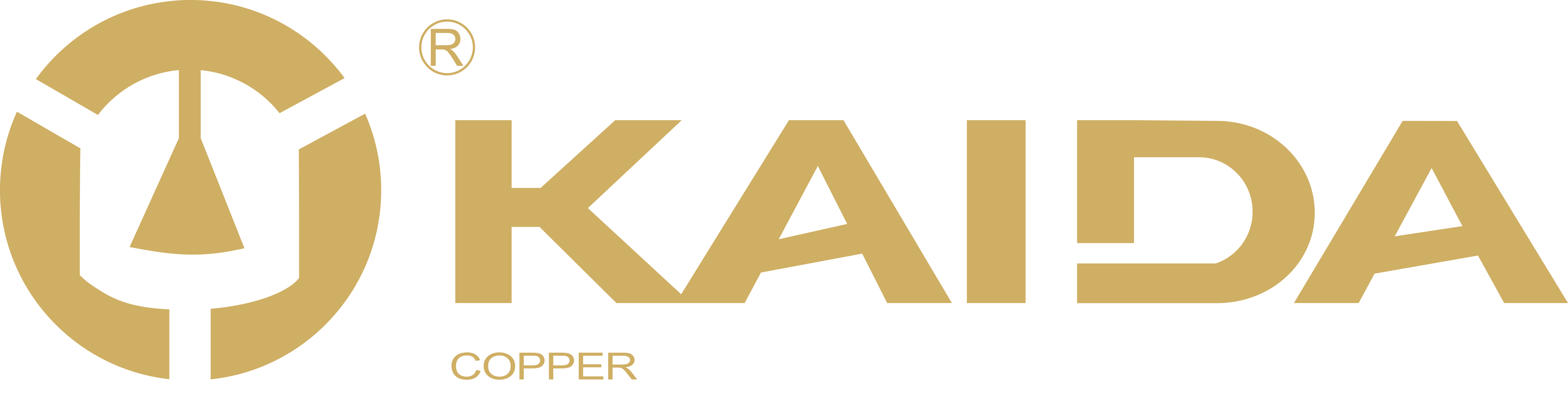
Advanced PVD Surface Treatment Center
Creating Durable and Lustrous Finishes for Premium Brass Products
A New Era in Brass Surface Treatment
KAIDA BRASS has launched its advanced PVD (Physical Vapor Deposition) facility
We provide consistent quality and customized solutions for brass products:
Beyond Tradition
Addressing limitations of electroplating in wear resistance and environmental impact
Color Innovation
Achieving metallic finishes beyond conventional techniques
Performance Enhancement
Combining artistic beauty with industrial strength
"Not just equipment installation, but a technological revolution tailored for brass products"
Advanced Equipment
Our PVD systems ensure quality surface treatment
CICEL PVD
German-engineered multi-arc magnetron system optimized for brass alloys
- Max processing size: Φ1800mm × H2200mm
- Sputtering targets: 27 units
- Temperature control: ±5℃
PlasmaClean
Ensures substrate cleanliness for coating adhesion
- Dual RF plasma sources
- Automated cleaning programs
- Multiple gas cleaning options
- 40% increased efficiency
QualityLab Pro
Comprehensive testing equipment for quality assurance
- Coating thickness measurement
- Adhesion testing
- Salt spray test chamber
- Color difference analyzer
Equipment Commissioning Progress
We are optimizing our systems to ensure performance
New Facility · Professional Standards
We've established standards for professional PVD treatment
Brass-Specific Process Development
- Premium equipment: CICEL multi-arc magnetron system
- Rigorous testing: 200+ brass substrate trials
- Class 10,000 cleanroom environment
- German engineering team support
Quality Commitments
- Coating adhesion: Class 5B (ISO 2409)
- Corrosion resistance: >72h neutral salt spray (ASTM B117)
- Environmental compliance: Zero cyanide wastewater · RoHS/REACH
- Heat resistance: 400℃ without discoloration
Current Capabilities
We offer mature PVD surface treatment technologies and processes
Production-Ready Technologies
Classic Finishes:
Performance:
- Hardness: HV 800-2200 (adjustable)
- Heat resistance: 400℃ without discoloration
- Coating thickness precision: ±0.2μm
- Electrical conductivity retention: >90%
2025 Technology Roadmap
- Enhanced-wear-resistant nanocomposite coatings (Q3 launch)
Hardness increased to HV 3000+, wear resistance improved 3x - PVD + laser etching texture process (R&D)
Micron-level precision textures for enhanced design - Antibacterial brass treatment (Patent pending)
99.9% antibacterial rate for medical & food applications - Smart temperature control system (Q4 launch)
±5℃ precision for sensitive components
Technology Development Milestones
Our PVD Treatment Gallery
Explore the finishes of our advanced PVD technology
Key Application Areas
We specialize in PVD treatment for brass products in these sectors
Application | Typical Products | Core Value |
---|---|---|
Architectural | Door handles/Facade elements/Bathroom fixtures | Weather resistance/Fingerprint-proof/10-year color guarantee |
Premium Homeware | Cookware/Lighting/Art decor | Food-grade safety/Easy cleaning/Long-lasting beauty |
Industrial Components | Heat sinks/Conductive parts/Bearings | Enhanced wear resistance/Reduced friction/Heat tolerance |
Electronics | Audio panels/Connectors/Heat spreaders | High conductivity/EMI shielding/Corrosion resistance |
Gifts & Awards | Trophies/Commemorative coins/Premium pens | Luxurious finish/Permanent color/Unique designs |
Technology Partnership Program
Join us in exploring new possibilities for brass surface treatment
Joint R&D
Co-develop surface solutions for specific applications
Sample Testing
Free sample testing with technical analysis report
Process Optimization
Tailored treatment processes for your products
Strategic Partnership
Long-term collaboration for market development
Ready to Enhance Your Brass Products?
Contact us today to discuss how our PVD surface treatment can add value to your products
Request Consultation